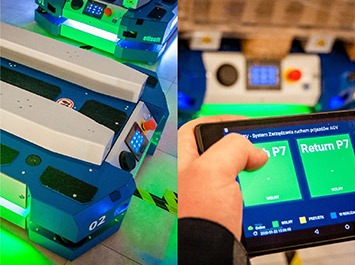
Robotization in retail & logistics – overview for 2020
26 May 2020
As far as saturation with robots is concerned, the Polish market is unfortunately at the end of the rankings, which is quite surprising if we take into account, for example, Polish GDP (where we have 22nd place in the world) or Human Development Index (Poland with 32nd place in the world).
In 2014, roboforum.pl wrote that “Poland, with the value of the index at 18, is at the bottom of the ranking. Not only the leading countries in this respect, but also countries with a similar level of development, such as Hungary or Slovakia, have a higher density of robotisation than Poland. The average robotization density in Europe is 4.4 times higher than in Poland (compared to the previous year, Poland reduced the distance to Europe by 1.1 points), while the global average is more than 3 times higher”. However, a lot has changed since 2014. According to IFR 74% of the new robots have been installed in 5 countries: China, Japan, USA, Korea and Germany. In industry, robot saturation has more than doubled (from 44 to 99 robots per 10 thousand people employed and from 200 thousand to 400 thousand robots per year), with a certain stagnation and lack of growth forecasts for the future.
What about the trade and logistics industry? The IFR has only recently included it in its reports, but according to one of them, it is in this segment that the increase in robotization is very impressive and amounts to 60% per year.
Types of robots used in trade and logistics
Robots used in trade and logistics can be divided into: arms (articulated, Cartesian, SCARA, PUMA, Tripod, delta…), vision systems (MVS or Machine Vision Systems) and mobile robots (AGV = Automated Guided Vehicles, AMR = Autonomous Mobile Robots).
Robotic arms
Robotic arms replace human hands in packaging processes, orientation of products on tape or in a box, picking of complex orders and marking of products or packages. Among these solutions the following are particularly popular:
- Parcel induction – correcting the orientation of the product on the tape or in the packaging based on image analysis and arranging packages on the tape in the desired way.
- Case packing – packing and consolidation of orders in boxes/cartons
- Goods-to-Person Fulfillment – preparing and delivering ready-made sets (products, documents, packaging) to the packing station, where the final work is done by a person.
Vision systems
Machine Vision systems automatically control the work done by man or other machines, by analyzing the image recorded by industrial cameras. If a deviation from the assumed standard is detected (e.g. a sticker in the wrong place, lack of one of the elements included in the set, wrong orientation of the element in the box or an illegible barcode), the system starts a programmed action, e.g. stopping the production line, marking the element as defective, triggering an alarm or redirecting the product to a side line. Vision systems often support the work of both robotic arms and mobile robots and are also used in product safety systems (traceability).
Machine Vision systems allow you to automate quality control processes. Thanks to their use, it is possible to:
- Reduce the number of complaints through a comprehensive, automated control of the correctness of installation.
- Verification of compliance of products with the specification, including verification of the product version or completeness.
- Machine measurement of assembly accuracy or product positioning precision.
- Automation of fault indication through notification, marking of the defective product and control of the production line
- Automatic control of mandatory equipment (helmet, mask).
- Automatic, non-contact measurement of employee body temperature.
- Support for theft detection by self-detection based on historical data and real-time face analysis.
- Detection of anomalies in the production and storage hall space – obstacles, abandoned objects, high temperature and others.
Mobile robots
Recently, mobile robots have been pushing people out of storage space en masse. There is a shortage of warehouse workers throughout Poland, and warehouses are often located on the outskirts of cities or even in the fields and they are struggling to ensure workforce. Especially during the summer, holiday or flu season. Relatively high wages, regulated by law for night work or public holidays, and the risk of loss of workforce – all this makes automated internal transport systems seem to have the best years ahead of them.
Among mobile solutions in trade and logistics we can distinguish the following groups:
- P2P transport (Point-to-Point) – AMR trolleys carrying baskets around the warehouse, driving shelves with assortment put into them by a man, or an intelligent rack. All this makes the human work of handling transport unnecessary.
- Intralogistics transport systems based on AGV, automated rollers and integration with MES storage systems. In this case, in addition to eliminating manpower during loading and transport, the systems also take care of automatic mission sequence management or traffic optimization, and during reduced traffic (e.g. at night), they sort the contents of the warehouse and they move e.g. pallets, which are primarily intended for loading, closer to the terminals in order to shorten the time of loading.
- Automatic data collectors – that is, mobile stations performing inventory by scanning labels or RFID tags, as well as analysing unstructured image. They are able to notice the lack of goods on the shelf or the placement of the wrong product in the wrong place.
As you already know, mobile robots can be divided into AGV (Automated Guided Vehicles) and AMR (Autonomous Mobile Robots)
AGV systems enable:
- Reducing the cost of internal transport.
- Replacing forklift trucks, operators and operators with autonomous AMR vehicles.
- Optimization of transport orders in real time.
- Assignment operations such as sorting to robots during reduced traffic hours.
- Elimination of additional human and infrastructure costs in onerous, harmful and special working environments.
- Reduction of additional labour costs related to absenteeism, night work and weekends.
AMR systems, on the other hand, enable:
- Automated material transport.
- More frequent and accurate data collection in industrial and commercial environments.
- Even 2-3 times better picking performance.
- Reducing labour costs.
- Effective management of growth, seasonal occupancy and staffing needs.
“R” like robotization
Both robot arms, Machine Vision systems and mobile robots are part of the rich Euvic’s offer to the retail sector. Cooperation with partners such as Etisoft or Zebra Technologies has a positive impact on the optimization of store operations and better use of resources and human capital. Robotization of the retail industry allows to create ideal environments for shoppers, and additionally frees employees from repetitive, monotonous tasks. It helps to eliminate problems with stocks and prices, and to comply more easily with accepted standards and requirements, which in turn contributes to improving the overall efficiency of the store. As I wrote at the beginning, in recent years there has been a significant increase in robotization both in retail and logistics. However, all indications are that the investments made in this area are only the beginning of real development, and the biggest players still have a real revolution ahead of them. I have already given some examples of automation in the retail sector, in my article about technological trends in retail but today, once again, I would like to emphasize that there will be no turning back from robotization. After all, wherever there are repetitive processes, the robot’s work will always be cheaper and more accurate than human work.
The author of the article is Bartłomiej Łatka, an expert on retail and logistics.
back